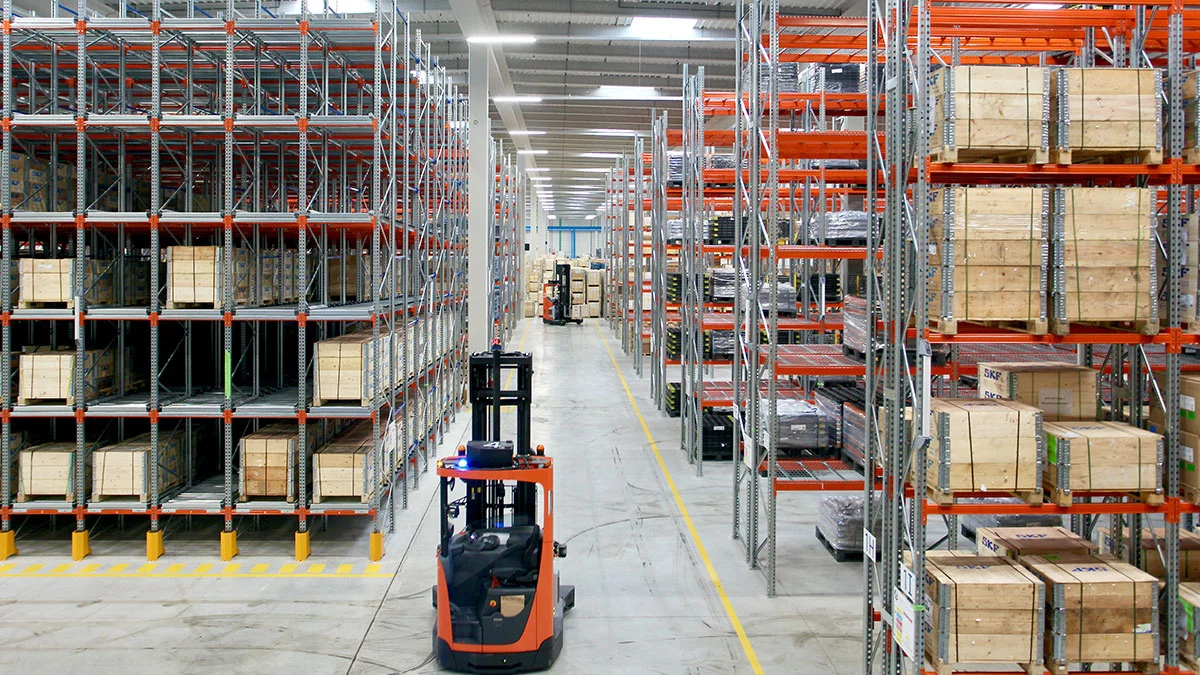
Inventory Optimization: Balancing Supply and Demand in Warehousing
Inventory management is a critical aspect of any warehousing operation. It involves the efficient control and tracking of stock to ensure a balance between supply and demand. Effective inventory optimization strategies help businesses streamline their operations, reduce costs, and improve customer satisfaction.
In this article, we will explore the concept of inventory optimization and its significance in balancing supply and demand in warehousing. We will delve into various aspects of inventory management, including strategies, best practices, and frequently asked questions (FAQs) to provide a comprehensive understanding of this crucial topic.
What is Inventory Optimization?
Inventory optimization refers to the process of maximizing the efficiency and productivity of inventory management within a warehousing system. It involves finding the right balance between stocking enough inventory to meet customer demand while minimizing excess inventory that ties up capital and increases carrying costs.
By implementing effective inventory optimization techniques, businesses can ensure that they have the right products in the right quantities at the right time. This helps in avoiding stockouts, reducing inventory holding costs, and improving overall operational efficiency.
Importance of Balancing Supply and Demand
Balancing supply and demand is crucial for maintaining a healthy inventory level. When supply exceeds demand, excess inventory accumulates, leading to higher holding costs, increased risk of obsolescence, and reduced cash flow. On the other hand, insufficient supply can result in stockouts, dissatisfied customers, and lost sales opportunities.
Proper inventory optimization enables businesses to find the equilibrium point where supply matches demand effectively. It allows for smoother operations, cost savings, and improved customer satisfaction. By aligning inventory levels with customer demand patterns, businesses can minimize stockouts, reduce carrying costs, and enhance their overall competitiveness.
Factors Affecting Inventory Optimization
Several factors contribute to the successful optimization of inventory in a warehousing environment. Understanding these factors is crucial for developing effective strategies and implementing best practices. Let’s explore some of the key factors below:
Demand Forecasting
Accurate demand forecasting is essential for inventory optimization. By analyzing historical data, market trends, and customer behavior, businesses can make informed decisions regarding inventory levels.
Lead Time Management
Efficient lead time management ensures that products are delivered within the expected timeframe. By reducing lead times, businesses can maintain lower inventory levels and respond quickly to fluctuations in demand.
Economic Order Quantity (EOQ)
EOQ helps in determining the optimal order quantity that minimizes total inventory costs, considering factors such as carrying costs and ordering costs. By calculating the EOQ, businesses can make data-driven decisions regarding order quantities and frequency.
Just-in-Time (JIT) Inventory Management
JIT inventory management aims to minimize inventory holding costs by receiving and using inventory just in time for production or delivery. This approach reduces storage requirements, lowers carrying costs, and enhances operational efficiency.
Vendor Managed Inventory (VMI)
VMI is a collaborative approach where suppliers manage the inventory levels of their customers. By allowing suppliers to monitor and replenish inventory, businesses can reduce the burden of inventory management while ensuring a steady supply of goods.
Cross-Docking
Cross-docking is a logistics practice that involves unloading goods from an inbound shipment and directly loading them onto outbound transportation, with minimal or no storage time in between. This strategy reduces the need for storage space, accelerates order fulfillment, and optimizes inventory levels.
Warehouse Layout Optimization
Efficient warehouse layout optimization improves the flow of goods, minimizes travel distances, and maximizes space utilization. By strategically organizing storage areas, picking zones, and workstations, businesses can optimize inventory movement and reduce operational inefficiencies.
Technology and Automation in Inventory Optimization
Leveraging technology and automation solutions can significantly enhance inventory optimization efforts. Advanced inventory management systems, RFID tracking, and automated order processing streamline operations, improve accuracy, and provide real-time visibility into inventory levels.
Inventory Optimization Software
Inventory optimization software helps businesses analyze data, perform simulations, and generate insights for optimizing inventory levels. These software solutions often incorporate forecasting algorithms, demand planning tools, and inventory tracking capabilities.
Performance Metrics for Inventory Optimization
To measure the effectiveness of inventory optimization efforts, businesses can utilize various performance metrics. Key metrics include inventory turnover ratio, fill rate, order cycle time, carrying cost, and stockout rate.
Best Practices for Inventory Optimization
Implementing best practices is essential for successful inventory optimization. Consider the following recommendations to enhance your inventory management:
- Conduct regular demand forecasting and update it based on market trends and historical data.
- Establish strong relationships and effective communication channels with suppliers.
- Optimize lead times by collaborating with suppliers and improving logistics processes.
- Implement just-in-time inventory management techniques to reduce storage costs and improve operational efficiency.
- Leverage technology and automation solutions to streamline inventory tracking, order processing, and reporting.
- Continuously monitor key performance metrics to identify areas for improvement and make data-driven decisions.
- Regularly review and adjust safety stock levels to align with changing demand patterns.
- Train employees on proper inventory handling, storage, and retrieval techniques.
- Foster a culture of continuous improvement and encourage feedback from employees and customers.
Frequently Asked Questions (FAQs)
Q: How does inventory optimization help in balancing supply and demand?
Inventory optimization ensures that businesses have the right amount of inventory to meet customer demand while minimizing excess stock. By finding the right balance, supply and demand can be aligned, leading to cost savings, improved operational efficiency, and customer satisfaction.
Q: What are some common challenges in inventory optimization?
Common challenges in inventory optimization include inaccurate demand forecasting, long lead times, inadequate safety stock levels, inefficient warehouse layouts, and limited visibility into inventory levels. Overcoming these challenges requires a holistic approach and the implementation of appropriate strategies.
Q: How can technology help in inventory optimization?
Technology plays a vital role in inventory optimization by providing real-time visibility into inventory levels, automating order processing, enabling accurate demand forecasting, and facilitating data-driven decision-making. Inventory management systems, RFID tracking, and demand planning tools are examples of technologies used in inventory optimization.
Q: What is the role of performance metrics in inventory optimization?
Performance metrics provide valuable insights into inventory management effectiveness. Metrics such as inventory turnover ratio, fill rate, order cycle time, carrying cost, and stockout rate help businesses assess their performance, identify areas for improvement, and make data-driven decisions to optimize inventory levels.
Conclusion
Effective inventory optimization is a critical component of successful warehousing operations. Balancing supply and demand through accurate demand forecasting, lead time management, safety stock planning, and the implementation of best practices enables businesses to optimize inventory levels, reduce costs, and enhance customer satisfaction.
By considering the various factors influencing inventory optimization and implementing the recommended strategies and best practices, businesses can achieve operational excellence and gain a competitive edge in today’s dynamic market.